RFID Product Customization Expert – Your Exclusive OEM/ODM Solution Partner
In 2024, the global RFID tag shipment volume has surpassed the milestone of 50 billion units. More and more application scenarios are calling for RFID to have more functions and forms, empowering digital upgrades and business transformations. Our rich experience and professional team can provide you with first-class services and rapid support!
In the rapidly evolving landscape of RFID technology, businesses demand more than standardized products—they require tailored solutions that precisely align with application scenarios and enable swift market responsiveness.
As a professional player with rich expertise in RFID industry, we leverage deep technical mastery, rigorous end-to-end production management, and a robust network of high-quality manufacturing partners to deliver one-stop OEM/ODM services, from conceptual design to mass production and delivery.
About RFID+X Transponder Concept
- RFID+ LED
- RFID+ Sensor
- RFID + Capacitor
RFID+X technology is an innovative solution that deeply integrates traditional RFID tags with electronic functional components (such as sensors, LEDs, capacitors, etc.). Through the collaborative design of chips, antennas, and peripherals, the tag is upgraded from a "one-way data carrier" to a "environmental perception + interactive feedback" bottom-level perception unit in Internet of Things applications.
Perception layer: Unique electronic identity recognition, integrated temperature, humidity, pressure and other sensors, real-time collection of environmental data
Communication layer: RFID chip and antenna achieve wireless data transmission (UHF/HF/NFC)
Interaction layer: Dynamic LED display, capacitive touch feedback, energy harvesting module
Passive power supply breakthrough: By using radio frequency energy harvesting technology, sensors and LEDs can be driven to operate without an external power source.
What’s our offer on RFID/RFID+X Transponders?
1.Which RFID Transponders can we produce?
1.1 Which antenna types are supported?
- Copper Etched Antenna
Line width and spacing: Minimum 100um; Commonly, it is single-sided circuitry + printed via, supporting double-sided circuitry
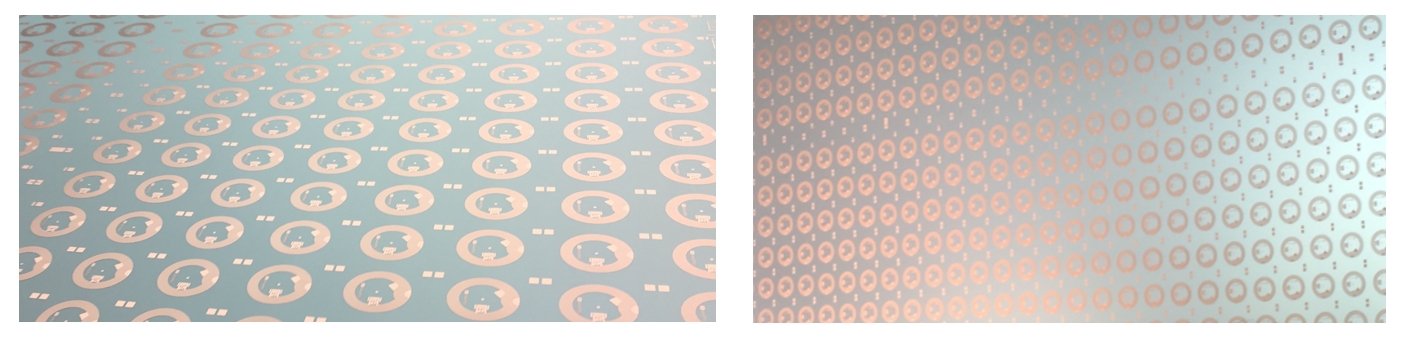
- Aluminum Etched Antenna
The general line width and diameter of the antenna is 200 um. For the HF antenna, it is a dual-sided circuit (supporting single-sided circuit + printed bridge); for the UHF antenna, it is a single-sided circuit.
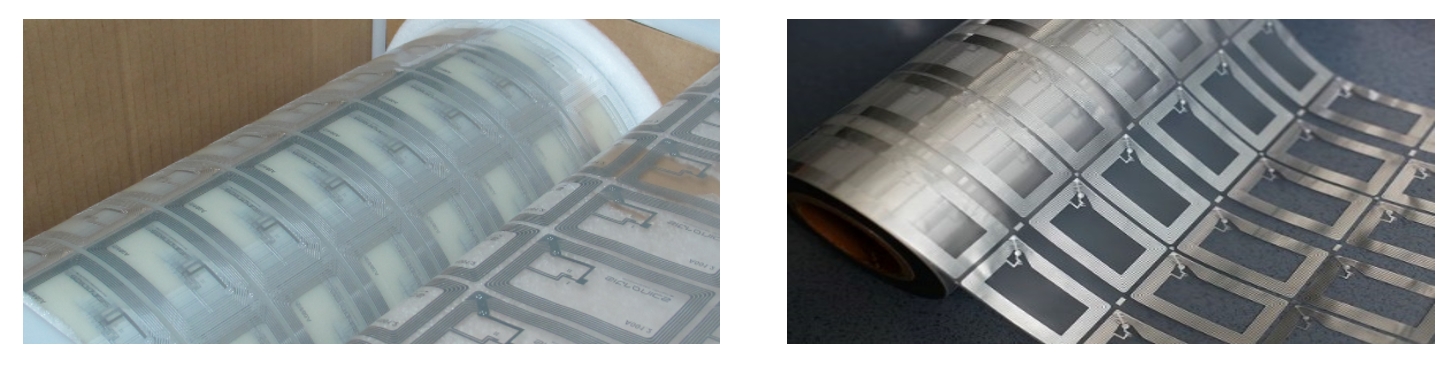
- Composite Substrate
Whether for RFID coupling tags or for non-contact card inlays; copper etching, aluminum etching and high-precision silver paste printing can all be perfectly combined.
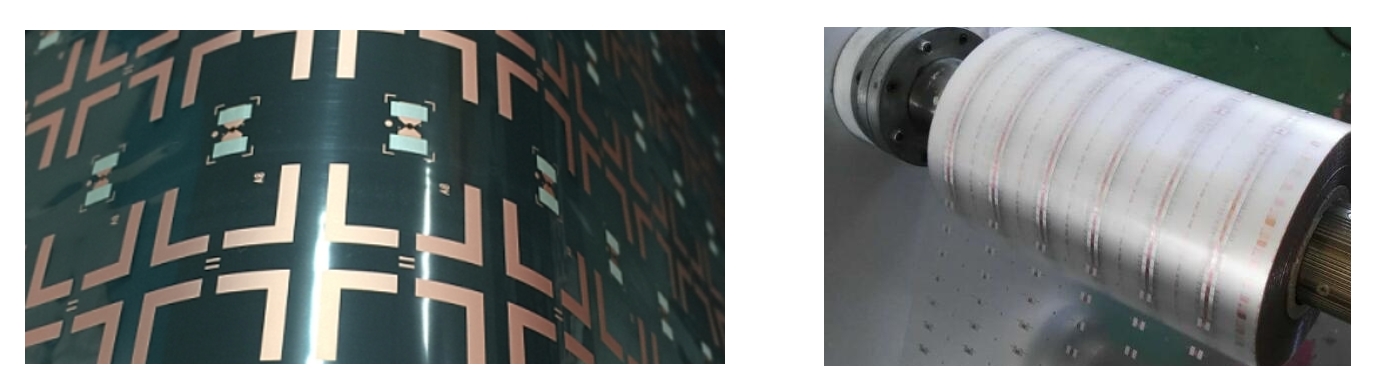
1.2 What are the common RFID antenna substrate materials and production technologies?
- PET Substrate
Aluminum/Copper etched lines: 38um, 50um are the common thicknesses; Aluminum etched antennas, the general line width and line diameter are 0.20mm; Copper etched antennas, the general line width and line diameter are 0.15mm.

- PI Substrate
Copper/Aluminum etched circuits: Aluminum etched antenna, generally with a line width and line diameter of 0.20mm; Copper etched antenna, generally with a line width and line diameter of 0.15mm.
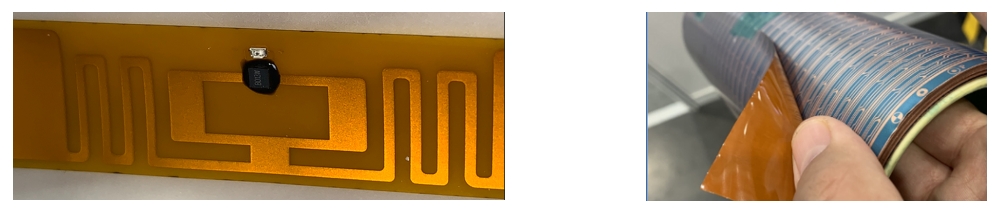
- Eco-friendly Paper Substrate
Printed circuitry, mature eco-friendly RFID tag antenna, using reliable "silver-buried-copper" conductive material, supporting both UHF and HF/NFC transponders; moreover, it also supports the paper-based UHF aluminum antenna process suitable for die-cutting technology, supporting the green earth. These two eco-friendly antenna technologies have high cost-effectiveness, mature technology, high production capacity, and are currently in mass production.
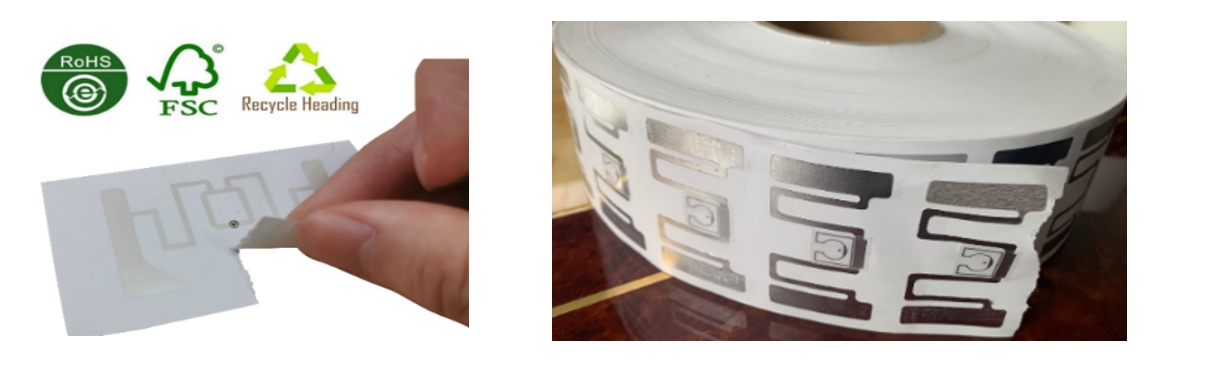
1.3 Which packaging technologies are supported?
- Flip Chip Bonding:
This is the mainstream packaging technology for RFID Inlays/Tags. It is a key process in the production of the largest volume roll material RFID labels in the industry.
Our factory is equipped with top-notch production equipment such as German Muhlbauer DDA 40K, TAL15K, etc. for surface mount machines.
We are providing OEM services for the world's leading players in the industry. The RFID products you see or are using might have come from us.
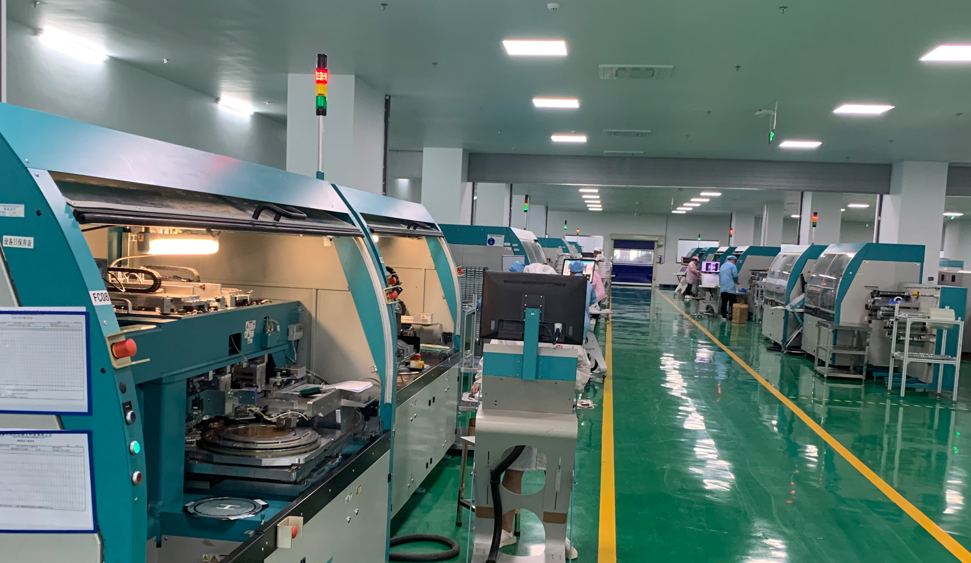
- For PI antennas used in applications demanding high temperature resistance and high RF performance, we offer two packaging processes:
Die Bonding + Wire Bonding for SMT process, and Flip Chip Bonding.
The RFID tags of PI antennas possess excellent high temperature resistance and RF performance. They excel in both miniaturization and high performance aspects, thus opening up diverse application possibilities. Many people only know that chips are bonded to transponders through SMT process, but few are aware that RFID chips can also be bonded to antennas through Flip Chip bonding.
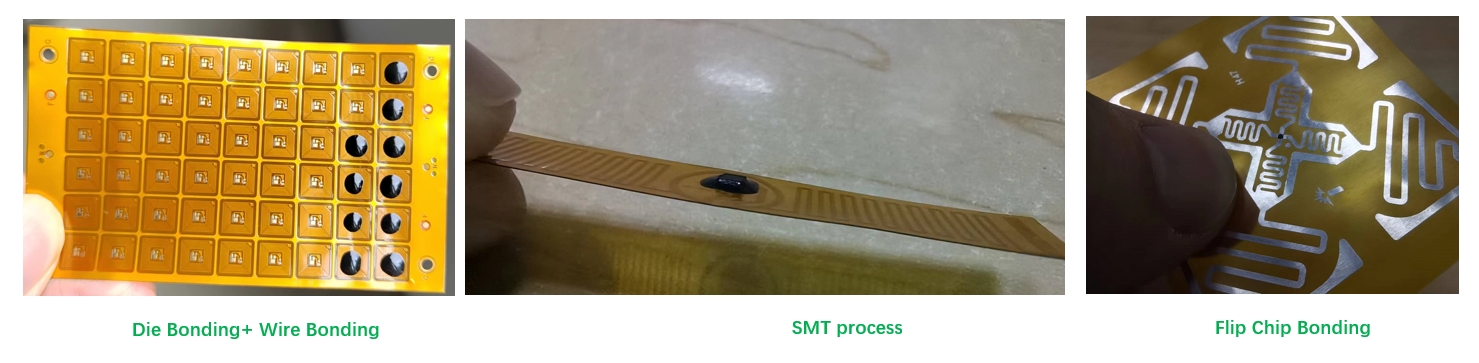
2. What unique services can be provided?
- Component (such as LED, capacitor) reverse-bonding packaging:
On the roll material RFID antenna, enhance the performance and functional diversity of your RFID tags! We are proud to support numerous industry partner companies, making your tag products more competitive. We can provide production capacity of over 100K per day to support you!
- Support bonding production of electronic components within a large size range:
Minimum L300um * W300um * T100um (currently M8 chip is 0.302mm * 0.247mm); Maximum L2000um * W2000um * T500um
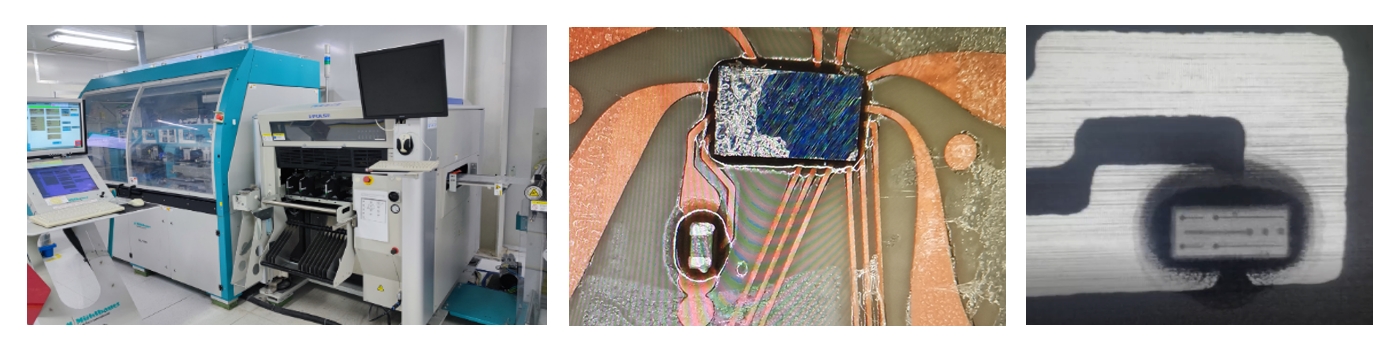
- Diverse forms of RFID + inlay such as RFID chips + LED, RFID chips + capacitors, etc.
For Passive LED emitting tags products, we have the ability to conduct 100% full-function online detection! We are providing support for the leading players in the field of passive RFID tags (without batteries) and sensor tags.
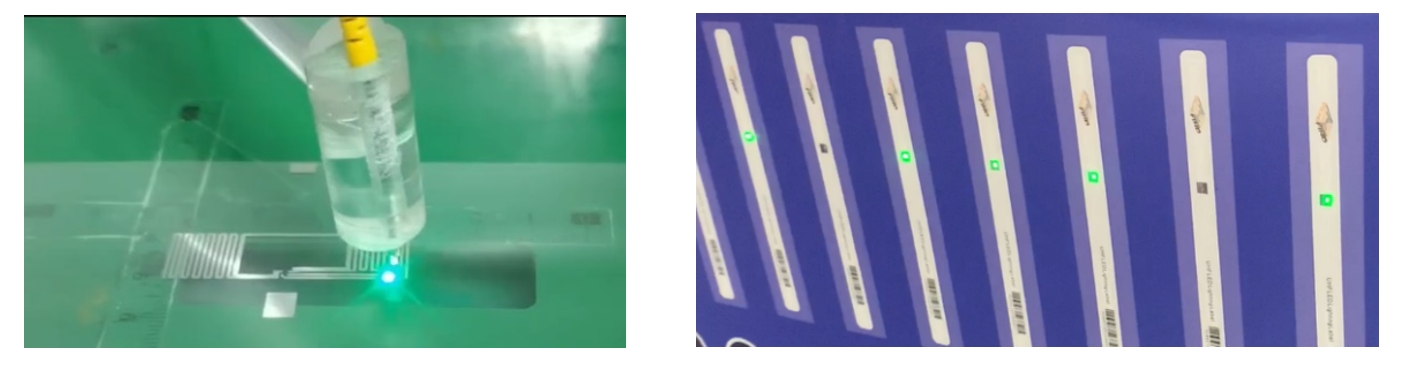
- Irregular pitch inlays flip chip
Is the Transponder pitch distance (MD Pitch) necessarily a fixed value? Can flip chip bonding production with variable MD values be achieved?
Most factories are variable, but our answer is yes! With efficient production methods, we can serve special RFID products such as contactless cards/RFID tickets. For single sheet products, some working space needs to be reserved at the bottom.
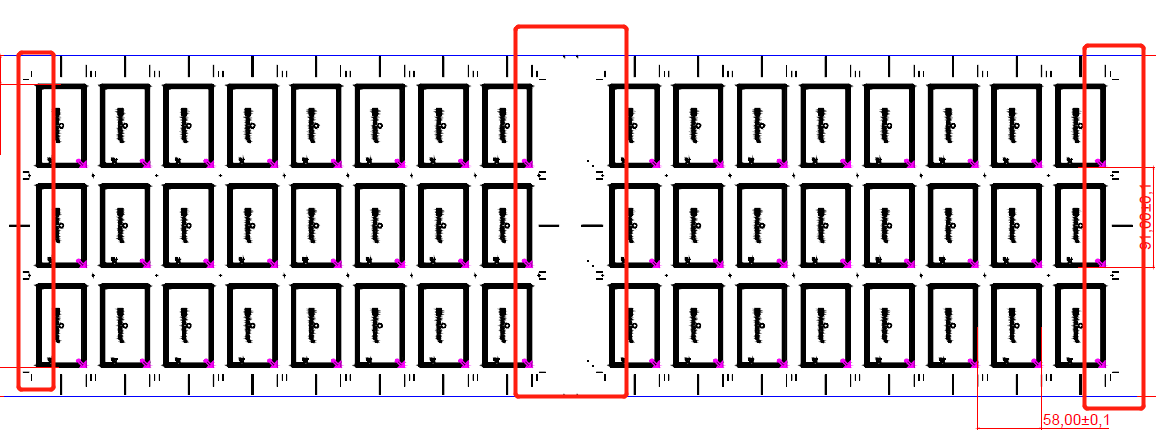
- Transponder shipping form: Not only does it support roll material, but also large sheet material. This enables customers to carry out post-production easily!
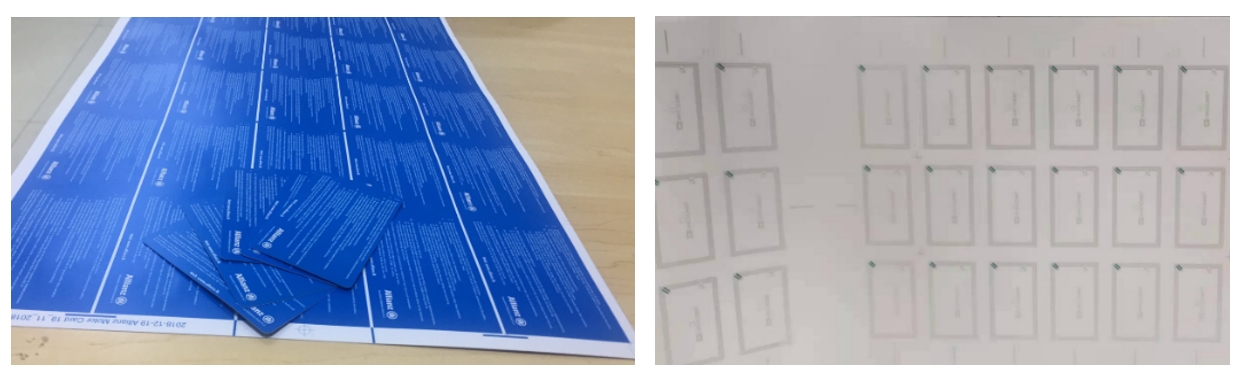
After flip chip bonding, the roll-inlay can be automatically cut into large sheets of inlay, meeting diverse production requirements, such as for the production of Plastic/Paper Card and other products.
- Adhesive application protection
On the web of substrate such as RFID Inlay, after bonding, components like chips, LEDs, capacitors, etc. are subjected to online adhesive application for curing, thereby achieving high-intensity protection for components on the substrate. After curing, the external shape of the adhesive application is uniform and consistent, and the dimensional accuracy is high. Epoxy curing.
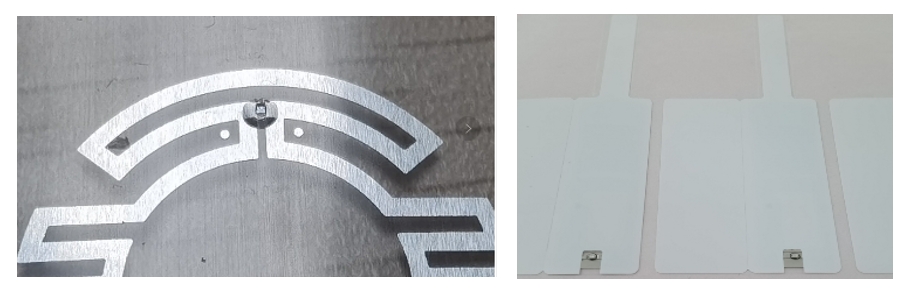
- Online detection of key elements
Not only is full online detection of the performance of transponders carried out, but also online detection of the appearance of key processes is required. We can achieve all of this.
100% comprehensive detection of the Frequency, Q Factor of the UID/TID;HF/NFC Transponder and the performance of the UHF Transponder, even allowing for batch data writing (chip initialization).
We have the world's top RFID testing machines (UHF: Voyantic Tagsurance, HF/NFC: Testram T8200Pro-G), which are installed on automated production equipment.
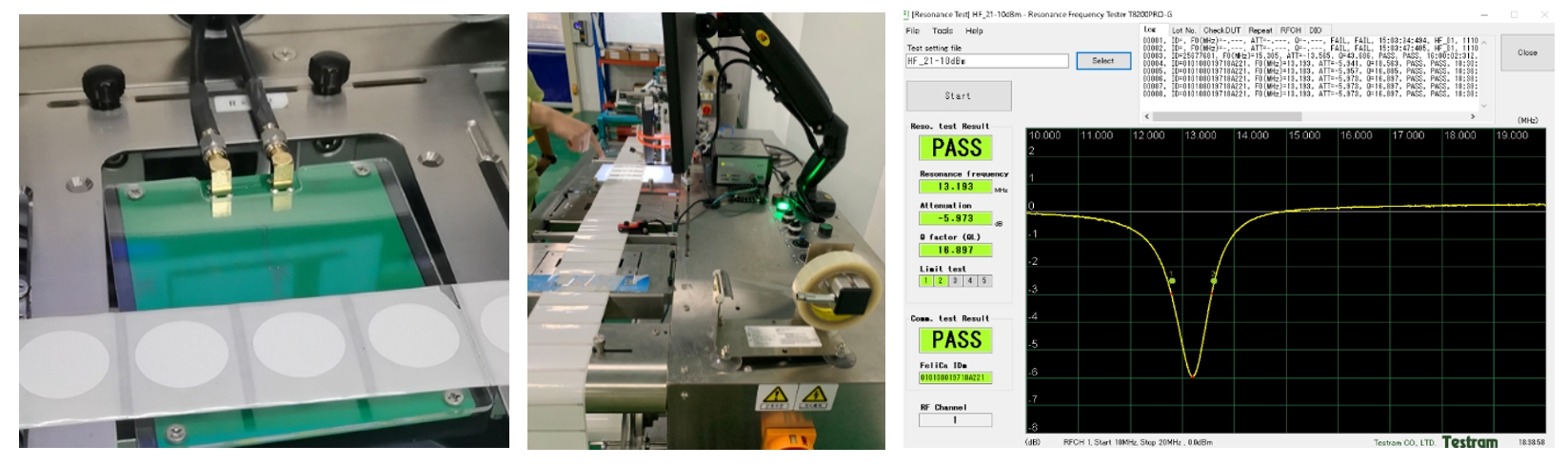
- Quality control of key processes (Inlay Flip Chip Bonding)
a. Chip Die Attachment Position
b. Reliability and strength of chip bonding
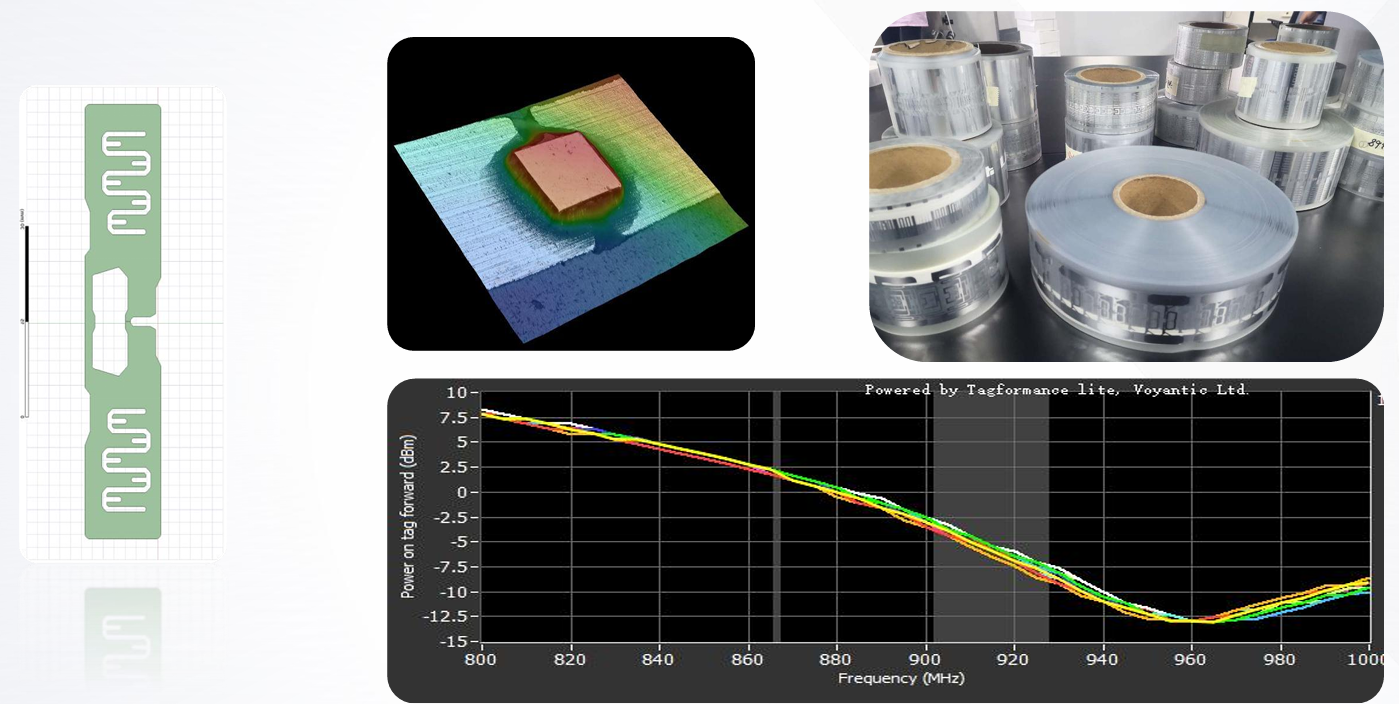

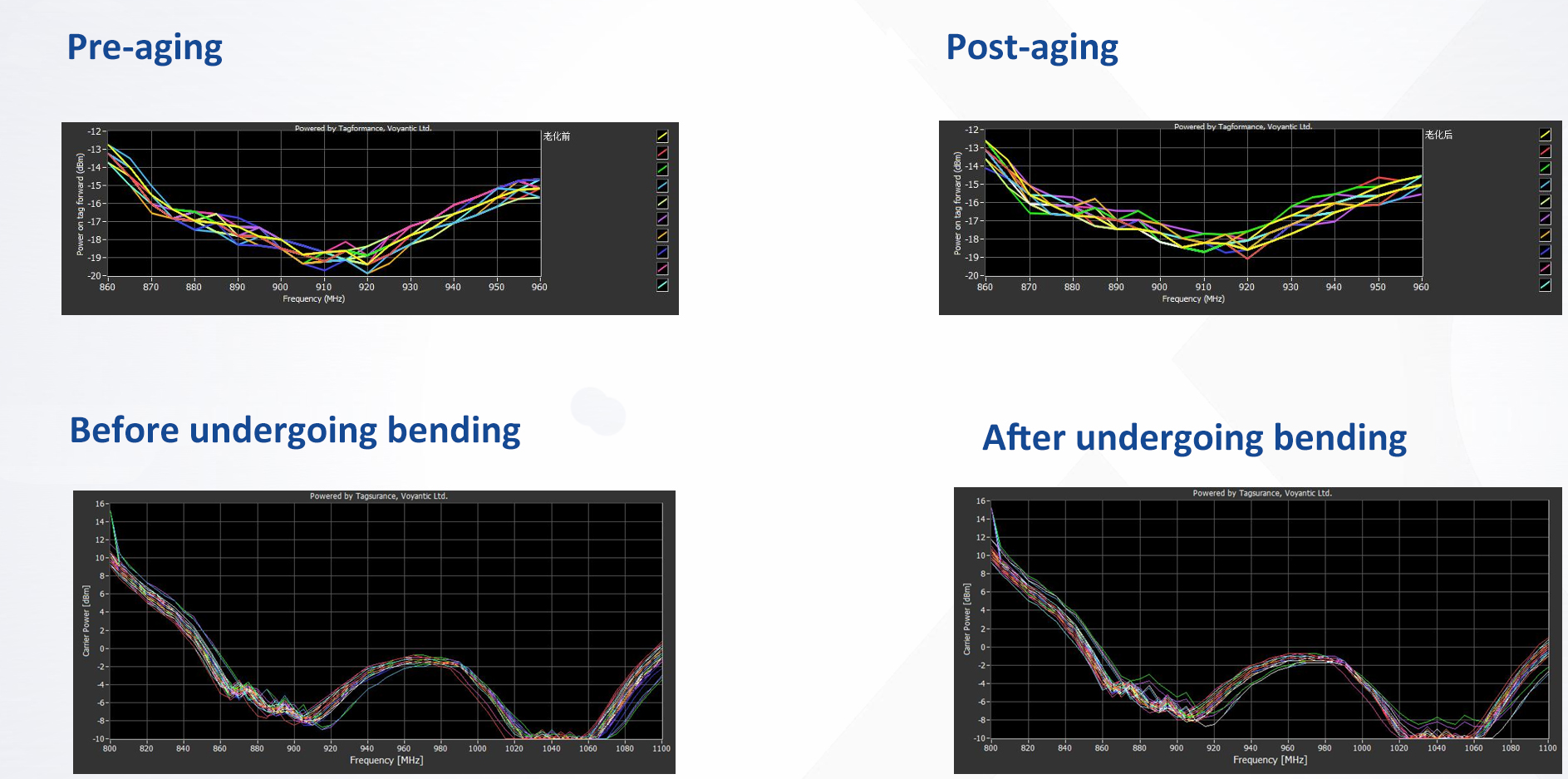
Why Choose Us?
-
1. Technology-Driven Production for Precision Customization
We are not just product suppliers but technical solution architects. From High-Frequency (HF) to Ultra-High-Frequency (UHF) tags, from anti-metal labels to flexible LED-integrated tags, our R&D team excels in RFID chip selection, antenna design, and encapsulation processes. We tailor solutions that balance performance and cost for industrial automation, smart retail, asset management, and more. -
-
2. Stringent Quality Control for Reliable Delivery:
We ensure compliance with client standards through rigorous quality management.
-
- Critical Quality Point Identification: Identify key process control points during design and prototype evaluation to eliminate batch risks.
-
- Full-Cycle Quality Assurance: Monitor critical parameters (frequency points, sensitivity, adhesive quantity) via first-article inspection, process inspection, and 100% performance testing.
-
-
3. Agile Supply Chain for Efficient Collaboration
By integrating resources across the Pearl River Delta and Yangtze River Delta (key manufacturing hubs in China), we ensure flexible production scaling: -
- Small-Batch Prototyping: Rapid sample delivery for quick solution validation.
-
- Scalable Production Capacity: Support mass orders up to tens of millions of units.
-
- Value-Added Services: Custom printing, data pre-writing, and more.